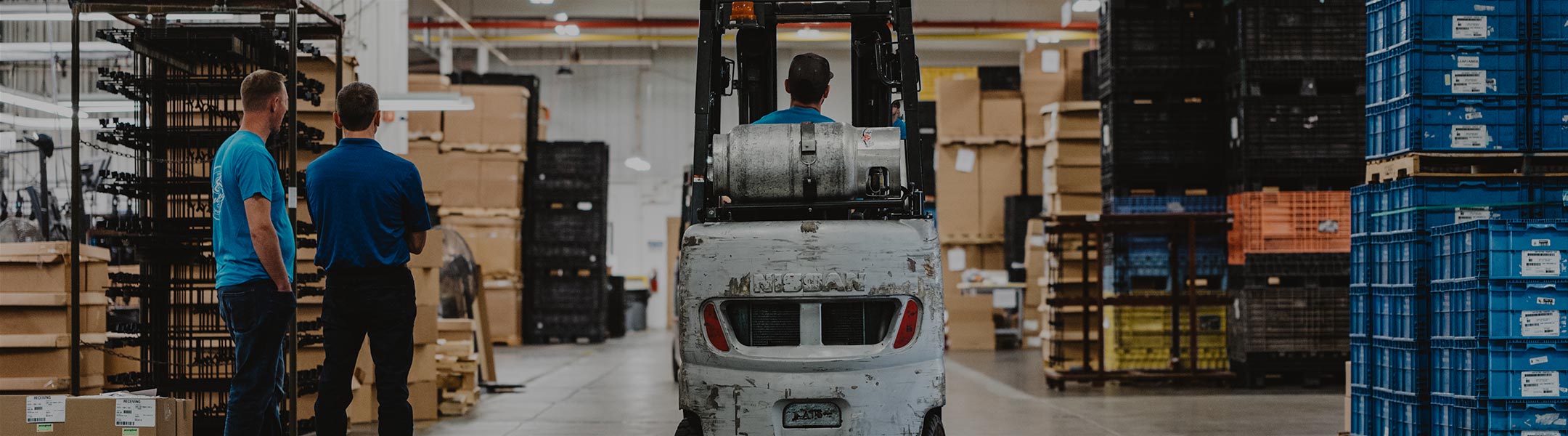
Get your copy of the 7th Annual State of Smart Manufacturing and hear from 300+ manufacturers in this new survey report!
For a monthly digest of expert insights, data points, and tips like the ones in this article.
In the modern manufacturing landscape, the synergy between plant floor operations and enterprise systems is the linchpin of a truly connected, intelligent production environment. At the foundation of this ecosystem, automation and control systems gather the vital signs of the manufacturing processes, but their true potential is harnessed only when this data informs the broader organizational objectives facilitated by ERP and MES.
Achieving this level of integration is not without its challenges, requiring a robust framework and adherence to industry best practices. In this blog post, we'll cover the blueprint and strategy for assessing your current state and building fundamental knowledge to streamline communication between automation and control systems and enterprise business systems.
Catalog Existing Systems and Infrastructure:
Data Flow and Storage Analysis:
Evaluate Current Data Structures:
Identify Communication Protocols:
Assess System Health and Maintenance:
Cybersecurity:
Edge Layer: At the edge, data is raw and often vast in quantity. Sensors, control systems, and local edge devices are responsible for collecting real-time data regarding machine status, product quality, environmental conditions, and operator interactions. Examples include temperature readings, machine operating states, energy consumption metrics, vibration levels, and much more.
Data Characteristics at Edge:
Edge Data Communication Needs:
MES/MOM Layer: The MES (Manufacturing Execution System) or MOM (Manufacturing Operations Management) layers translate granular plant floor data into actionable information. Examples include work order status, production counts, downtime incidents, quality metrics, inventory levels, and much more.
Data Characteristics at MES/MOM:
MES/MOM Data Communication Needs:
ERP Layer: ERP (Enterprise Resource Planning) systems synthesize information from across the enterprise to inform strategic and financial decision-making. Examples include sales forecasts, production scheduling, inventory valuation, procurement data, financial data, and much more.
Data Characteristics of ERP:
ERP Data Communication Needs:
A connected and intelligent production environment, formed through the synergy between plant floor automation and control systems and enterprise business systems, is one of the big goals of any modern manufacturing operation. To make this a reality, automation and control systems must gather the data from the manufacturing processes, but then that data must inform the broader organizational objectives usually facilitated by ERP, MES/MOM, and QMS.
But making this goal a reality is not easy and not without many challenges. Getting started toward building a robust framework using industry best practices requires a thorough assessment of your current situation. It also requires that you understand the fundamental approaches to data communications between automation and control systems and enterprise business systems. This is the place to start.
In my next blog we’ll take a closer look at edge computing and how it fits in with the overall approach required to build the synergy between the plant floor systems and the business systems. In the meantime, read this guide on leveraging a cloud-based MES.
This article was previously published by Harneet on MESA (Manufacturing Enterprise Solutions Association) International’s website.