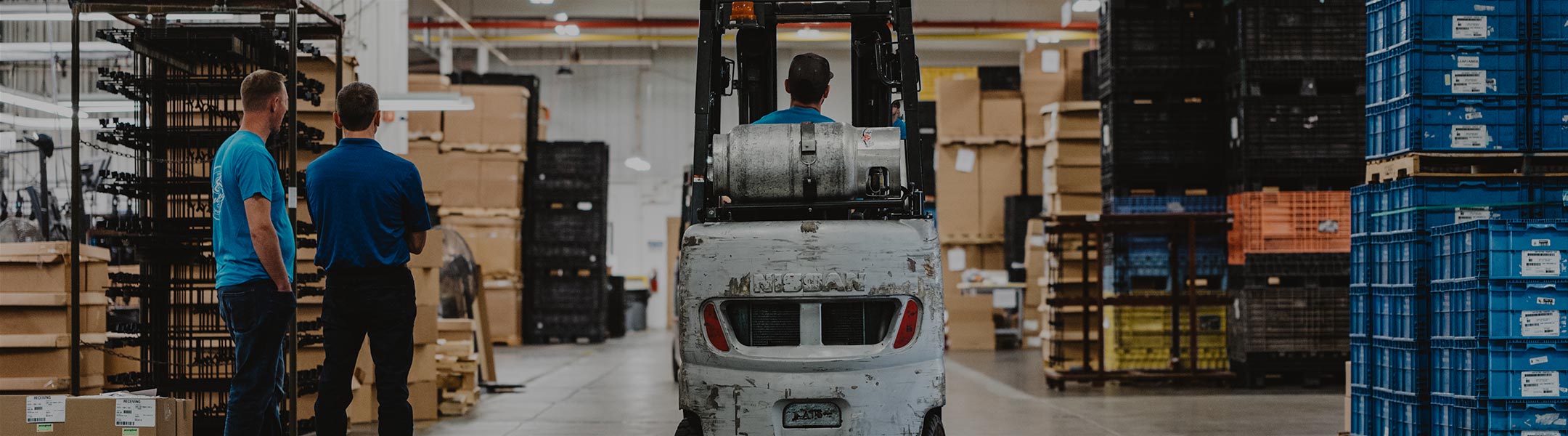
Get your copy of the 7th Annual State of Smart Manufacturing and hear from 300+ manufacturers in this new survey report!
For a monthly digest of expert insights, data points, and tips like the ones in this article.
By now, you’ve heard about the Industrial Internet of Things (IIoT). You may have even talked about it with your team but, if you’re like a lot of small to mid-sized manufacturing companies you are still in the early stages of investigating what IIoT means to your business.
That’s just it: you need a solid business reason (or reasons) to look seriously at the major technology evolution but you shouldn’t wait too long. LNS Research conducted a survey on IIoT adoption and nearly 53 percent of respondents have investigated or plan to invest in IIoT technologies by the end of 2017.
So how do you go about building a business case? A good place to start is on how IIoT will be used to drive efficiency, productivity, and quality. Below are four possible use cases that may help you:
1. Monitoring Assets in Operation:
In looking at your maintenance strategy for your machines and equipment, IIoT can be applied so you can monitor your assets while they’re in operation. For example, a bottling plant may fill thousands of bottles per minute and has hundreds of small motors. These motors typically aren’t monitored individually and follow a break-fix/replace approach. A large bottling facility recently that adopted IIoT technologies monitored these motors and discovered that micro stoppages from these motors accounted for one of the top downtime sources in the plant. By applying improved maintenance approaches to these motors, unplanned downtime was reduced by over 10 percent.
2. Increasing Product Safety:
An effective clean-in-place (CIP) process is one area where manufacturers can decrease or increase the risk associated with product safety. One large beverage company is using IIoT to rethink CIP. Rather than having plants locally assume that a production line is clean after a CIP activity is complete, the company will use the IIoT to provide global visibility of CIP and move to a model that measures cleanliness continuously, with the CIP ending when the line is clean. Typical turnover times are four hours per line. The company anticipates 50%+ reductions in turnover times, while simultaneously and dramatically reducing food safety risks by having a central repository of CIP performance.
3. Managing Recipe Variation:
Brewing beer is a complex process that includes almost infinite variations in recipes. One of the largest craft brewers in the U.S. recently engaged in an IIoT project using machine learning and historical process data to solve a batching problem that was resulting in a major quality issue and the loss of entire batches. The brewmasters thought the problem was the relationship between pressure and temperature; it turned out to be an issue with the timing of batch processes determined by natural variances in yeast. Using data collected, the brewmasters built a model to alter the recipe and optimize batches on previously unknown relationships. With the new process established, they eliminated lost batches for this quality issue and recaptured two weeks of extra capacity per lost batch.
4. Reducing the Cost of Quality Testing:
Quality testing and validation comes at a cost and is often a significant contributor to the total cost of quality incurred by a company. Because of these costs, quality best practices dictate that instead of testing every finished product, industrial companies should monitor the production process itself. By ensuring the process is error-proof, the outcome is consistent quality levels. IIoT and smart connected products are changing this game. One smart connected products company is using new connectivity and intelligence capabilities in the end product to conduct quality testing during production and feedback is being used for additional quality improvements.
Discover more IIoT use cases by downloading the LNS Research Infographic: Make the IIoT and Digital Transformation a Reality.
Source: LNS Research