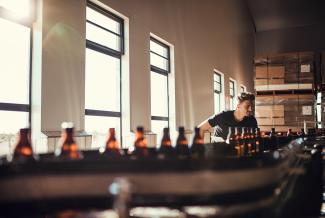
Get your copy of the 7th Annual State of Smart Manufacturing and hear from 300+ manufacturers in this new survey report!
Imagine if you could spend more time installing smoke detectors and less time putting out fires on your plant floor?
A cloud-based software solution is the key to unlocking best practices in processing quality and traceability for food and beverage manufacturers. Having a complete food safety management system built in the cloud gives you a proactive, risk-based approach to safety issues so you can spend time where it matters.
Download the white paper to discover the benefits of this approach as well as best practices like:
This paper highlights how food safety management systems enable best practices in food and beverage processing quality and traceability.
Today’s ever-increasing frequency and cost of food and beverage recalls harm not only the companies directly affected but potentially everyone in that industry. The ripple effect prompts calls for more stringent regulations and more rigorous documentation requirements for everyone, and the Food Safety Modernization Act signed into law in early 2011 gives the FDA the authority to require additional documentation.
We increasingly see consumer marketing and tracing for certain types of foods. But food processors don’t need to track from the farm. From a regulatory standpoint, processors only need to trace one-up and one-back, but even that is easier said than done.
To meet current and anticipated documentation and lot-tracking requirements of the USDA and FDA, all processors/manufacturers must be able to rapidly identify and track every single ingredient in their products through processing, packaging, and shipping to the exact customer location. They must be ready to respond at any time — and within hours — if they are asked to produce documentation of a product’s or ingredient’s history one-up and one-back in the supply chain.
Leading food processors are turning to innovative software solutions that help them achieve this level of traceability, seeking both granularity and speed in order to respond and react confidently and quickly to documentation or audit requests. But traceability is just one tool in the food safety toolbox. A comprehensive food safety management system includes the processes and programs to prevent as well as respond to a food safety issue.
A complete food safety management system enables total process visibility, real-time data access, and a high level of documentation management. This comprehensive system limits the need for additional resources and time spent and also removes the stress from the threat of audits and recalls.
A cloud-based software solution is the key to unlocking best practices in food and beverage processing quality and traceability. To begin with, a cloud-based system is maintained and managed in a highly secure environment off-premises, and real-time information is accessible anytime, from any location.
What does this mean for food and beverage processors/manufacturers?
Standard practices in traceability are largely reactive. If a quality or safety problem is identified in an ingredient or food product, the distributor or retailer (or perhaps a regulator or consumer) notifies an account representative who notifies the quality teams. Quality teams often wade through paperwork and numerous systems trying to identify the root cause, gather processing and shipment paperwork, analyze the problem and, if appropriate, notify the supplier of a compromised ingredient.
Then employees manually search large amounts of paper records to try to understand where and when the problem started and which ingredients were impacted so they can remove them.
Because quality is key to business health, the tracing process often requires an all hands on deck approach and pulls employees from other projects for a significant time. The longer a resolution takes, the higher the risk to your business and to consumer health.
Now, consider what a company with the Plex Smart Manufacturing Platform experiences in the same scenario.
Plex enables quality professionals to spend more time installing smoke detectors and less time putting out fires. When a quality problem is identified, the distributor logs onto Plex (even if the distributor does not subscribe to the system) and creates a problem report, noting the unique identification number, batch number, or barcode scan. The problem ticket triggers an alert in the system. Quality management staff automatically receive the ticket, along with a complete traceability tree for the problem product, including all ingredients.
If there are multiple complaints, the system can aid in a root-cause analysis by identifying commonalities. With the click of a mouse, the quality team can direct all or some of the ingredients within the identified batch to be quarantined inside the software, preventing their further use on the production floor. Then the software quarantines the inventory not yet consumed and all finished goods still in stock, and identifies any shipped products that may need to be recalled. Notifications are immediately sent to all distributors and customers.
Without the use of technology, the entire process typically can take days and if you are lucky, hours. With Plex, the same result is achieved in just minutes.
This scenario generates faster, more accurate results but it also eliminates hours upon hours of manual labor, minimizes the possibility for human error, eliminates business interruptions, and reduces risks to the public. Instead of just tracking documents about quality or mimicking paper-based systems, today’s technology manages and tracks all steps of production, measures and records data, and follows processes in real time.
Additionally, if a series of supply chain partners are using Plex, anyone with access to the system and appropriate permission can trace product data to the very smallest units and quickly view raw materials data more than one-up and one-back in the supply chain.
A leading frozen meal manufacturer develops, produces, and markets premium, fully cooked frozen entrées and sauces for the banquet, airline, passenger rail service, retail, and restaurant industries, as well as the military. The company is best known for having pioneered the “sous vide” (under vacuum) cooking process, which is viewed as a highly innovative technique among the professional cooking community. A user of the Plex Smart Manufacturing Platform, the company has complete online traceability of all 400 of its food products and the raw materials and recipes for each one.
The barcode on each lot or container automatically links to historical data for each raw ingredient. As the ingredient is used, that data is “rolled up” and linked to the barcodes for every product in which the ingredient is used.
Although the firm has never been subject to a government investigation or needed to initiate a recall, it is ready to respond quickly if necessary.
To ensure that its food safety system and traceability practices are world-class, the company employs the services of NSF Cook & Thurber, a nationally renowned food auditing firm. NSF Cook & Thurber audits the manufacturer once a year and assesses its food safety system, including its use of hazard analysis and critical control points (HACCP). As part of its work, the audit firm selects a given lot of an ingredient and must identify all of the finished lots to the first level of distribution.
In the case of an actual government inquiry, processors must accomplish this within 24 hours. The manufacturer is always able to identify all of the finished lots within minutes on the first pass. Imagine the benefit to customers and the industry if each manufacturer in a supply chain could respond in minutes instead of a day.
The flexibility and capabilities of world-class cloud systems not only enable best practices for today but also create an environment for manufacturers to continuously improve their quality and traceability processes — matching the spirit of the latest food safety legislation and customer requirements.
For example, with Plex, there is no limit to the information that can be stored. Users can move photos, documents, and more to the system, continuing to reduce the need for paper files, internal storage, and the delays that come from tracking files manually.
Also, plant-floor data can be used to improve decision-making. For example, processing automation quality reports can be administered and stored online so processing automation performance can be reviewed. Preventative maintenance programs can then be refined to best ensure quality production.
The Plex Smart Manufacturing Platform can be easily customized to meet unique quality challenges. For instance, a leading frozen food manufacturer wanted to ensure that certain raw materials, such as peanut oil, were identified as potential allergens. Plex was easily configured to automatically add allergen symbols on the barcode labels of those materials.
The ability of the Plex Smart Manufacturing Platform to support best practices like these helps leading food and beverage processors avoid worries about audits, investigations, and recalls, allowing them to focus on more important things, like maximizing productivity and profitability, and most importantly, producing safe, high-quality products.