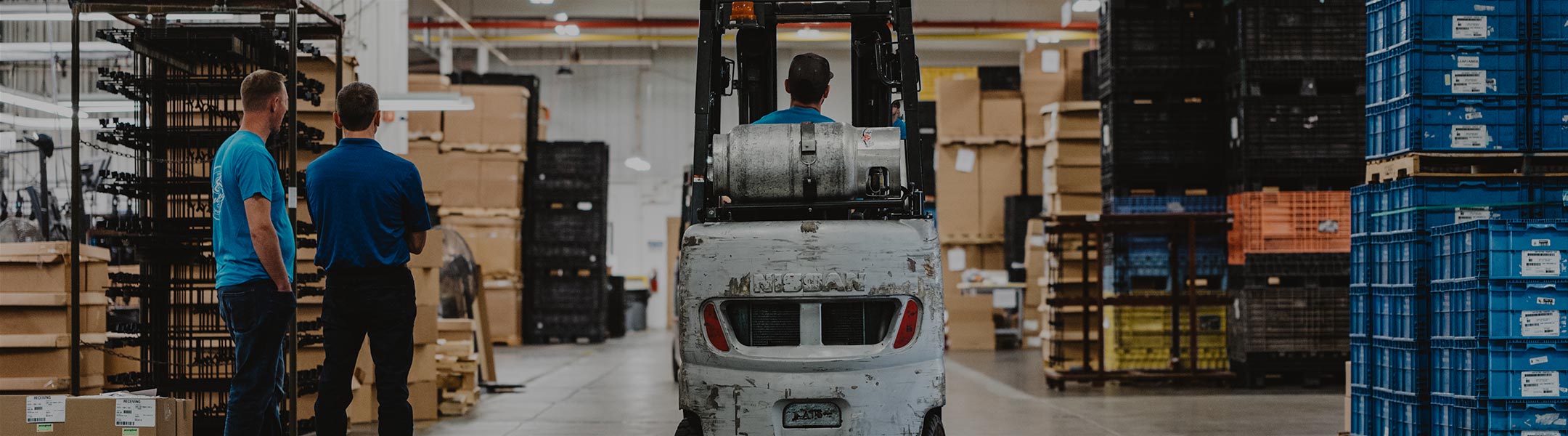
Get your copy of the 7th Annual State of Smart Manufacturing and hear from 300+ manufacturers in this new survey report!
For a monthly digest of expert insights, data points, and tips like the ones in this article.
We’ve compiled this list of warning signs many of our customers identified before moving to manufacturing ERP in the cloud. You know your systems are floundering when:
1. You spend too much money and time trying to keep your systems up to date and working smoothly.
Since your company has invested so much in existing systems, you continue to do what it takes to make them work. The problem is, whenever there is a software update or upgrade it creates operational challenges, sometimes even shutting down production. Costs keep rising and you are stuck in a vicious, never-ending maintenance cycle. You’re in the business of making products, not software maintenance and management.
2. You have difficulty pulling data out of transaction-based systems to determine how effectively your business is operating.
Most of the information you need is locked within disparate systems. That means someone has to do the work of collecting and compiling so you can use it. The problem is by the time you’ve done all of that, the information is out of date. You’d rather have your people focused on improving quality and on-time delivery—but management keeps demanding creation of more time-consuming manual reports.
3. You can’t pinpoint where materials are in the production process.
Your ability to accurately track materials as they flow through production and distribution steps is critical when it comes to responding to customer specifications and quality requirements. Without end-to-end traceability, it can take days to pinpoint problem components or ingredients to their source. And that costs you time and money, not to mention business risk to the public. If your systems don’t allow you to track and trace each step from receipt of materials to shipping, you need to find a system that does.
4. You can’t catch errors before products ship to customers.
You need to ensure high quality, while minimizing costs and mitigating the risk of recalls. Without an effective system that enforces quality processes, you are forced into reactive mode when there are errors. You likely have more scrap, waste, and returns than you want because you can’t effectively control quality during production at the manufacturing moment.
5. You aren’t sure how much inventory you have on hand or where materials are located in your facility (or facilities).
You likely have a larger work in process inventory than you’d like to maintain. Physical inventory checks are excruciating and labor intensive. Production slows down too whenever someone has to run around the facility (or call a supplier) to locate material. Manually entering in tracking data not only wastes time but opens up the opportunity for errors.