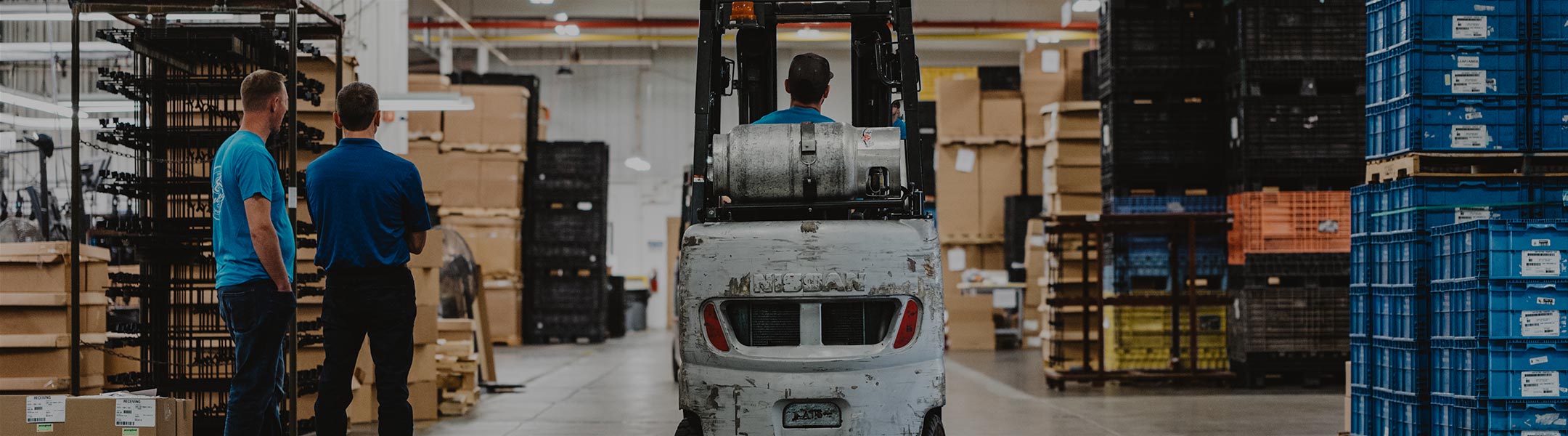
Get your copy of the 7th Annual State of Smart Manufacturing and hear from 300+ manufacturers in this new survey report!
For a monthly digest of expert insights, data points, and tips like the ones in this article.
It’s January – and for many companies, that means going through the rigors of the annual physical inventory. Is your company about to count everything in the warehouse, or just finishing up the process? Are you happy about it?
You shouldn’t be. No matter the result, the physical inventory process is difficult, disruptive, expensive and generally useless. Let me explain… There are only two valid reasons for doing a physical inventory count: 1) Record keeping is so bad that you don’t really know what you have on hand; or, 2) You are forced to do it by a parent company, auditor or some other outside force.
A physical inventory count often requires the suspension of everyday business for up to a day or more, as well as engaging people in the counting process that may not be adept at recognizing specific items, counting accurately, writing legibly on the count sheets, interpreting those count sheets and keying in the information accurately, or really caring about the validity of the process. Under these conditions, it is likely that the count will introduce as many errors as it corrects.
The result of the count, especially if it is done for accounting purposes, might be 98% accuracy – for example, meaning that the dollar amount of inventory determined in the count was within 2% of the presumed value, according to inventory records.
While this may be a good enough number for accounting, the actual accuracy of the inventory records is undoubtedly much lower. For example, if you count 100 items, the actual count might show that 50 of them are incorrect – but the pluses and minuses tend to cancel each other out and the sum total value is close to the expected amount. From an operational point of view, that means the accuracy is 50% - meaning that there is a 50-50 chance that you will find any given item in stock at the quantity your records say is there.
The objective, of course, is to keep better records. Ideally, each company should report inventory movement as it happens, as close to the event as possible, and preferably by the people that are handling the inventory. Automation can help with this process via bar codes, radio-frequency ID tags (RFID) and warehouse automation that can improve record accuracy while reducing the reporting requirements for the material handlers.
The best tool available for improving inventory accuracy is a process called cycle counting. A certain number of items are counted each day or week, and the count frequency is set such that more important items – ones deemed more valuable, more susceptible to theft or damage, more critical to operations or have the highest volume – are counted more frequently, but relatively the same number of items are counted each time. This may sound more complicated than it is, but it’s relatively easy to set up the counting process and then carry it out since it becomes a routine task.
The important thing about cycle counting is that it provides a better opportunity to identify the source of errors and eliminate them, improving accuracy over time. The count is completed by material specialists who are motivated to keep records accurate. The increased accuracy from this process can be monitored and documented, then used to convince the auditors that the expensive and disruptive annual physical is no longer needed – and your record accuracy will make operations go more smoothly, with fewer unpleasant surprises (such as shortages) and better customer service.