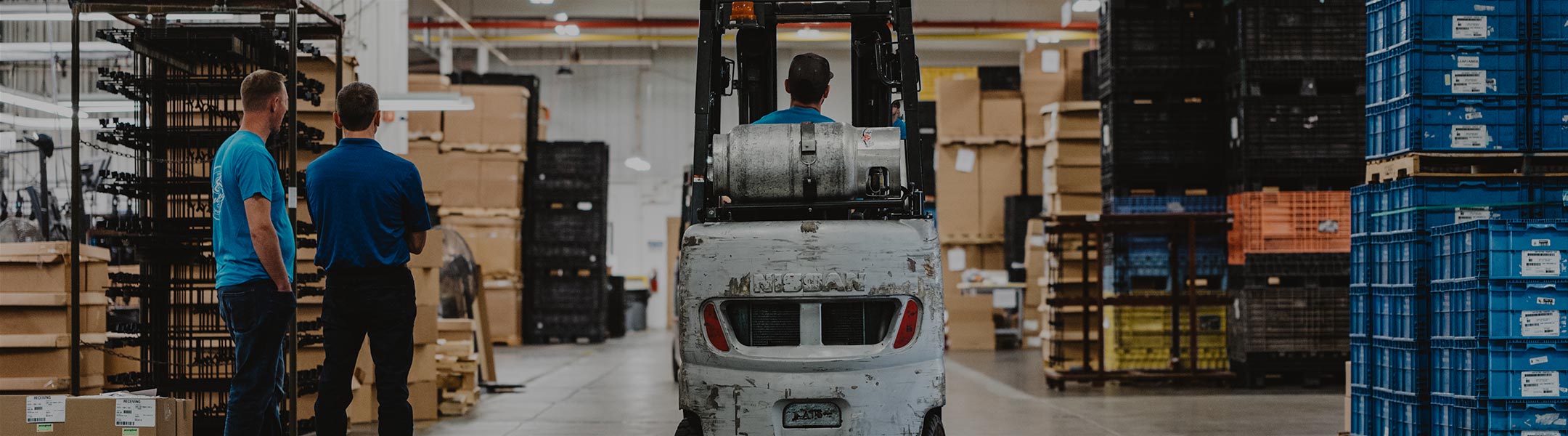
Get your copy of the 7th Annual State of Smart Manufacturing and hear from 300+ manufacturers in this new survey report!
For a monthly digest of expert insights, data points, and tips like the ones in this article.
We live in a global market. But when it comes to unskilled assembly-type jobs with a high labor content, let’s be honest: These are gone from the U.S. forever.
Any of this kind of work that comes back to North America will only be because automation removes the labor content, since our robots can perform “manual” labor cheaper and more reliably than untrained or unskilled workers in other parts of the world.
However, large and heavy products are expensive to ship halfway around the world and probably should never have been offshored in the first place. With a heightened awareness of total cost and supply chain risk, companies will logically source and build these kinds of products on the continent where they are sold. This means, however, that it doesn’t make any more sense to export this kind of product than it does to import them.
In a recent interview for MIT Technology Review, Harry Moser, head of the Chicago-based Reshoring Initiative, said: “Most of the products coming back (production that has been contracted offshore and is being brought back to U.S. factories) went away only recently, and often without much economic logic — it’s generally mechanical and electrical equipment that has some size and weight, such as transportation equipment, die castings and foundries. The cost is just too high to ship those.”
Foreign carmakers are building plants in the U.S., while Deere and Chrysler are building plants in China, to name just a few examples. The factories will land where the best combination of cost and convenience dictate. On the plus side for North American manufacturers, there are two factors that are now recognized much more than in the past:
Plant location and sourcing decisions are constantly shifting as economic, political and market factors evolve. It’s easy to see how decisions that made sense 10 years ago no longer add up the same way, and you can be sure that things will be different a few years from now as well. The best strategy is to maintain flexibility and continually watch these market forces so as to detect changes as early as possible.