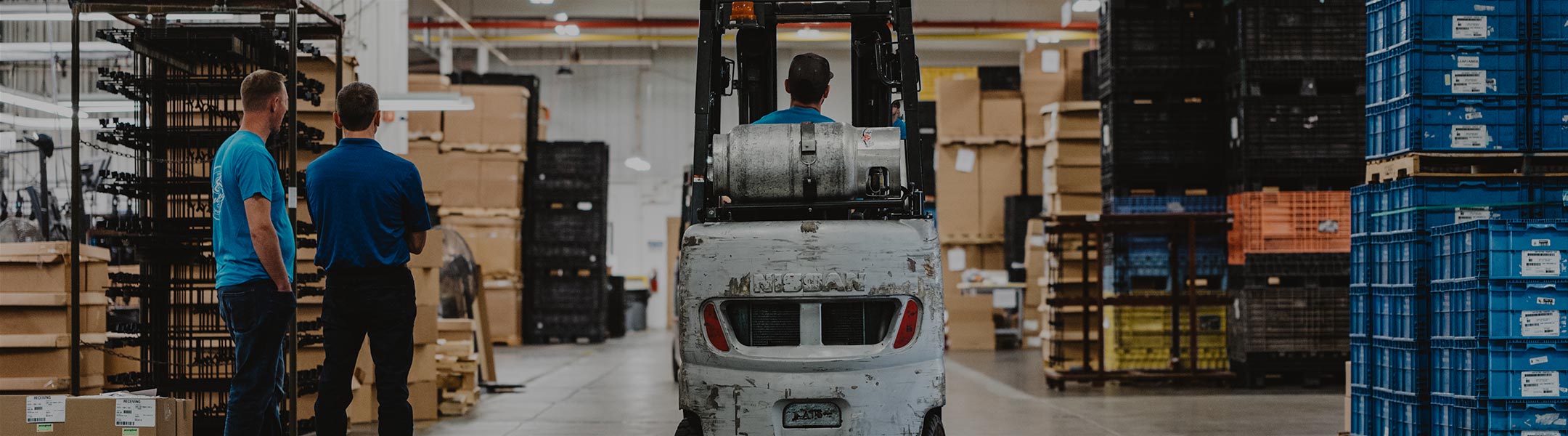
Get your copy of the 7th Annual State of Smart Manufacturing and hear from 300+ manufacturers in this new survey report!
For a monthly digest of expert insights, data points, and tips like the ones in this article.
So, you’ve decided to embark on an overall equipment effectiveness (OEE) project to increase equipment effectiveness and develop process improvements that maximize efficiencies. You’ve got your spreadsheets and clipboards ready (you don’t really need those, but more on that later). You’re ready to go. Now what?
When used right, OEE is a powerful tool that can provide valuable insights into where to focus improvement efforts. It’s often used as a tool within Lean and Six Sigma methodologies and is also used in conjunction with other tools as part of an overall process improvement strategy.
To get to these insights, it helps to understand the OEE KPI calculation and how it works. OEE is a calculation that tracks fully productive time as a ratio to planned production time. The formula for OEE is:
OEE = (Good Count x Ideal Cycle Time) / Planned Production Time
This formula yields a number that can be used as a benchmark for comparing performance across industries or from machine to machine. It can be used as a baseline for tracking the history of production runs to identify process improvements or reduce waste in specific assets.
There are three units of OEE, including Availability, Performance, and Quality. Each plays a role in arriving at the total OEE calculation. And each has a calculation to arrive at a value for that unit.
Availability counts the available run time divided by the total time. This value means that standard process stops such as changeovers and unplanned stops such as breakdowns are factored in.
Run Time = Planned Production Time – Stop Time
Performance captures small stops and slow-downs such as clearing jams, minor cleaning, and training issues. It’s where labor impacts the OEE calculation both in quality and quantity.
Performance = (Ideal Cycle Time x Total Count Produced) / Run Time
The quality aspect of OEE measures the volume of in-spec parts over the total number produced. It also includes reworks as out of spec.
Quality = Good Count / Total Count
By breaking down these specific categories, managers can identify problems specific to those areas. It allows them to target particular types of issues for improvement. And while the master OEE formula remains the same, breaking the metric down into these three components means that insights into underlying causes can be determined.
OEE = Availability x Performance x Quality
OEE is a widespread tool used in manufacturing to unlock insights. But others can be used instead of or as a complement to OEE and included in analysis later. One of these is Total Effective Equipment Performance (TEEP). In this metric, available time is based on 24 hours per day for the entire year. It also looks at availability, performance, and quality, but it considers availability to be a calculation of:
Availability = Actual Production Time / All Time
This result is multiplied by quality and performance to deliver the TEEP. Using TEEP in conjunction with OEE can render a deeper production analysis and allow for better forecasting and stronger improvement insights.
Back to those spreadsheets and clipboards. OEE is powerful either as a standalone tool or when used with others such as TEEP. As part of a best practices methodology such as Lean and Six Sigma, it can unlock insights to improve processes and increase efficiency. But why stop there?
Just because a company can track OEE manually, why should they? With software for smart manufacturing platforms, ERP, MRP, and MES, OEE can be fully automated. This means that availability, performance, and quality can utilize advanced analytics capabilities in real-time. And that same software can track multiple KPIs for OEE, TEEP, and more.
When combined with IoT technology embedded in equipment or retrofitted and communicated to the cloud, this combination of metrics and the analysis on the platform can unlock deeper insights and more accurate conditions for better decision-making and process improvements.
If you’d like to learn more about ditching your spreadsheets and conducting world-class OEE in your company, then let’s start the conversation.