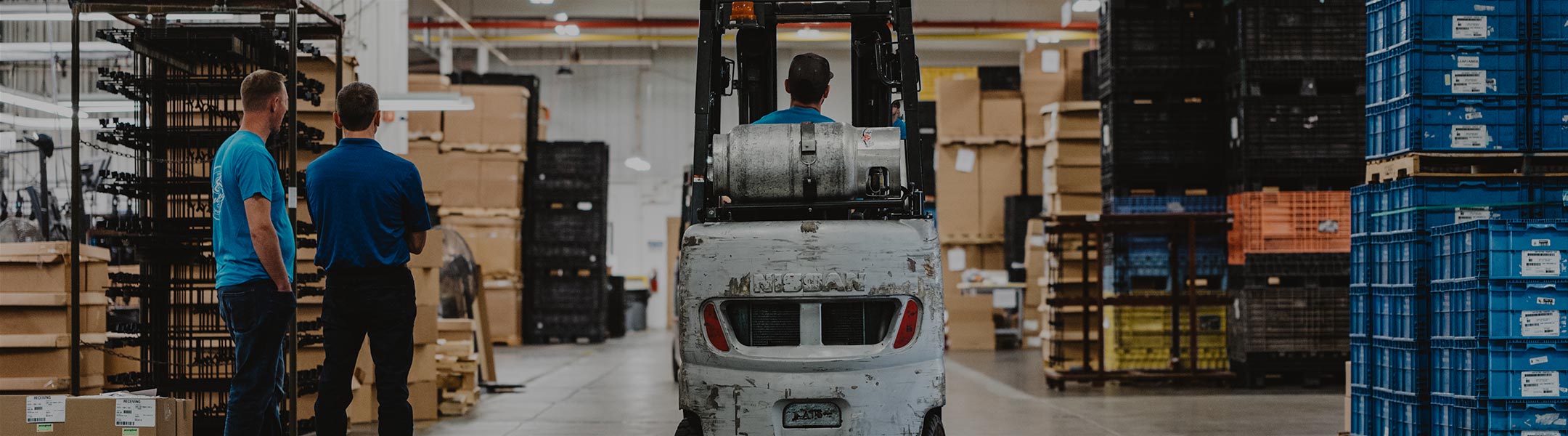
Get your copy of the 7th Annual State of Smart Manufacturing and hear from 300+ manufacturers in this new survey report!
For a monthly digest of expert insights, data points, and tips like the ones in this article.
What makes a good Quality Management System (QMS) tick?
After all, you want to be able to rely on a QMS to help you achieve and maintain the highest level of quality control and quality assurance while meeting the modern needs of your manufacturing enterprise. It’s a big ask from any software system, but when your QMS employs the Plan-Do-Check-Act method, or PDCA, it can turn your current state into your ideal state.
PDCA is a cyclical framework that can be applied to all internal processes, helping organizations deliver the highest possible quality to their customers. It’s a requirement in ISO 9001, one of the most common standards used by quality management systems across a variety of industries.
An effective QMS not only digitizes your data, but it also makes data-driven insights possible. Instead of dealing with manual errors and waiting for information that’s outdated before it even hits the spreadsheet, a QMS deploys real-time data. This helps companies connect, automate, track, and analyze operations using actionable information for repeatable and predictable quality.
Strong QMS software offers digital quality and compliance monitoring to create a closed-loop quality system. It utilizes methods like PDCA so you can implement continuous quality improvement faster than humans alone can accomplish.
Plan. Planning is a vital part of quality control and encompasses several elements. It starts with identifying the needs of your QMS stakeholders, which are key to scoping your QMS initiatives. The planning process also includes identifying and addressing potential risks, setting quality objectives, and anticipating changes to support continual improvement. The final step is to implement the support structure that’ll allow you to carry out your plans. Throughout the planning process, it’s essential that company leaders are committed to focusing on the customer, defining internal roles and responsibilities, and establishing a quality policy. This gives the overall QMS a fixed direction.
Do. Once established, the plan must be properly executed. A company will need to identify controls for quality management operations, consider product or service requirements, and develop designs. Any externally provided processes, services, and products also require controls. The ‘Do’ phase involves considering all the activities related to fulfilling your promise to customers and determining what’s required to deliver maximum quality.
Check. Make sure your planning and execution are meeting your needs and functioning as planned. You should monitor, measure, analyze, and evaluate internal QMS processes. Also verify that the products and services you deliver to consumers are meeting their standards for quality and satisfaction. Internal audits are a reliable method for checking the effectiveness of the QMS. The management review process assesses all the monitored data to make any necessary changes that address issues.
Act. Action involves fixing any issues found in the previous step. Improving internal processes and eliminating the causes of actual or potential nonconformities are the overall goals here. It’s a fulfilling step that feels more tangible than conceptual, enacting real change with clear impacts.
Plan (again). It’s time to run it back. This process is repeated to ensure that potential issues identified in the ‘Check’ phase or corrective actions taken in the ‘Act’ phase are incorporated into planning and meet the updated requirements in the ‘Do’ phase. Repeating the process unlocks continuous quality improvement into the future.
Deploying the PDCA cycle within a QMS creates a closed-loop digital record that strengthens quality processes. This helps ensure compliance, improve customer satisfaction, and enable continuous improvement. Whether you’re disappointed in your current QMS or are generally looking to take your quality strategy to the next level, thinking in terms of the Plan, Do, Check, Act stages will feel like a revelation.