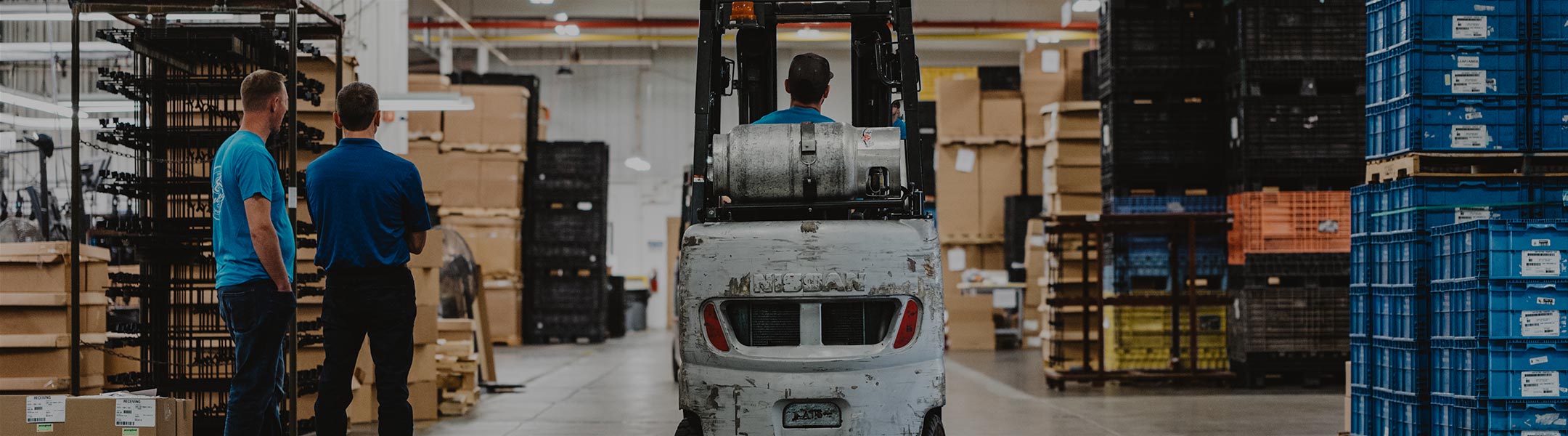
Get your copy of the 7th Annual State of Smart Manufacturing and hear from 300+ manufacturers in this new survey report!
For a monthly digest of expert insights, data points, and tips like the ones in this article.
While the last few years have seen significant events like COVID-19 and other disruptions impact profit for companies in every industry, staying profitable and maximizing profit is a never-ending pursuit.
Companies often audit, implement improvement initiatives, and pressure suppliers to lower the cost of raw materials to increase their bottom line. But hidden in the weeds is a cumulative set of issues that has more impact than many realize.
These issues create an undercurrent that erodes profitability. And often, managers miss other important cues that add to significant cost centers that impact profit. The cumulative threat of death by a thousand cuts is just as troubling, if not more so.
Manufacturing companies are under intense pressure to increase efficiency and profitability while improving product quality and reducing lead time. Many companies need help achieving these goals due to challenges that may not be obvious.
Each of these hidden challenges can reduce cash flow and impact profit. But together, they can add up to significantly impact a company's bottom line. Here are seven ways that profit can go missing.
All the negative variables above reduce profit by impacting the external supply chain. But companies have an opportunity to mitigate these forces, bring the supply chain under control, and put profit back to the bottom line.
A robust Manufacturing Execution System (MES) like Plex MES monitors, tracks, and controls the entire manufacturing process from the raw material stage to production and shipping. The dynamic software operates at or near real-time, enabling the management of supply chain processes throughout the entire production cycle.
It allows simple, low-code automation through customized apps to automate complicated process flows and drill down to the most important steps. The system can also be configured to capture operational data and apply it to quality checks, work instructions, change orders, and other workflow components.
The key to this process is connectivity through advanced edge computing. Machine assets organize and analyze data on the factory floor the moment it’s generated, reducing latency and powering automation. Plex MES is interoperable with other software and creates an ecosystem whereby your internal manufacturing supply chain has accurate, real-time, and actionable data.
When your production processes are agile, automated, and optimized, it creates a ripple effect that flows to the external supply chain.
Plex MES secures these internal forces with automation and analytics so you can focus on solutions to improve and empower the rest of the supply chain with real-time data.
Learn more about empowering your supply chain with automation and software in our Smart Manufacturing Software Buyer’s Guide.