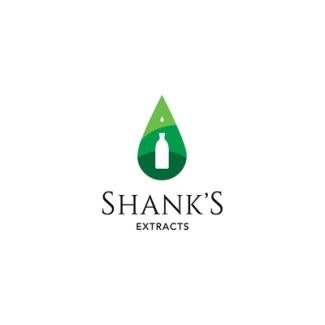
Get your copy of the 7th Annual State of Smart Manufacturing and hear from 300+ manufacturers in this new survey report!
Shank’s Extracts, Inc. supplies vanilla extracts, other extracts, natural and artificial flavors, food colors, and syrups to a wide range of industrial, private label, and grocery customers worldwide. The company is headquartered in Lancaster, Pennsylvania with a 110,000 square feet facility for operations, sales and customer service, manufacturing, packaging, and distribution.
As a private label manufacturer, Shank’s Extracts faces complex supply chain, production, and quality challenges. There are many moving parts across several products that all have to work in concert with each other in order to meet customer demand. The company currently has about 2,400 active formulas for its vanilla and other extracts with 3,300 SKUs for finished goods—and growing.
“We've had steady growth over the years as we've picked up new customers one by one. I believe this is due to the fact that we have a really good reputation of doing our work, doing it well, and doing it quietly. As a private-label manufacturer, we're always trying to keep our name out of it but our work in front of our customers,” said Jeff Lehman, President of Shank’s Extracts.
Focusing on quality management and on-time delivery is an all-encompassing endeavor, which is why Shank’s decided to move from its legacy ERP system to cloud ERP. Two of the company’s subsidiaries are in different states and an on-premise solution just couldn’t provide the kind of access Shank’s needed.
“We were tired of upgrading software. Every time we’d do an upgrade on the software, we had to get a new hardware system. We outgrew this model—our Wi-Fi system couldn’t handle it and our internet speed slowed to a grinding halt. It was time to move to a different model,” said Lehman.
Though some employees were used to having an ERP system and data on site, the team set out to find a cloud-based ERP system. The benefits offered by the cloud—accessibility, no major IT hardware investments, no recurring maintenance costs, and always-current ERP—outweighed any concerns in the end. After seeing the Plex Manufacturing Cloud in action, the team knew it found a solution that would meet its needs.
“When we also saw Plex’s redundant, bank-vault-designed, and fault-tolerant data centers with security like Fort Knox, we knew our data was in good hands,” said Jennifer Rayner, ERP Analyst for Shank’s.
The other critical factor that contributed to Shank’s decision was Plex’s origin on the shop floor.
"Whether you’re making widgets or food, there are a lot of similarities like with quality processes. Plex has also made signifi cant investments in food and beverage manufacturing so we were confi dent with our decision,” said Robert Murphy, Shank’s CFO.
Before Plex, jobs were entered into the system after the fact so getting an accurate read on what was happening in production proved difficult. Shank’s soon realized the decision-making power in capturing data from the shop floor with Plex.
“We can see all of the work being done at the production line in real time and I have access to all the data. This has really improved our inventory control and management,” said Rayner.
Now Shank’s has detailed information on dates for raw materials received, inventory on hand, and the exact location for inventory in its facility. Additionally, the company can accurately look at direct material usage for cost of goods and details into rejects and scrap factors to determine if the company is losing materials in the production process, and why, so operators can take immediate corrective action.
Quality is one of the key areas where Shank’s seeks to differentiate itself from competitors for private label business. Many customers look for suppliers who can meet stringent quality compliance. Murphy says the checks built into Plex help the company maintain quality rigor and identify issues quicker.
“Because all of our analytical testing, product attributes, and quality data reside in Plex, we can easily trace the source of production materials in seconds, isolate issues faster, and automatically generate audit reports.”
Since quality control plans and compliance documentation are embedded in the system, Plex has made the entire quality certification process faster and more accurate. Before Plex, the company’s quality systems regulatory coordinator would spend two to three weeks preparing documents for an audit. She would stack documents on a conference table organized in piles based on what she thought the auditor would request. During an audit, she would have someone run to the table to get the appropriate paperwork requested by the auditor. Now she goes into an audit with a laptop computer and quickly searches and finds nearly anything the auditor requests in real time.
“Quality is the lifeblood of our business because the demand is not just from a compliance standpoint but most importantly from our customers. Our ERP system has to support quality standards because it's how we remain competitive. Plex gives us the edge over other manufacturers who can’t meet customer requirements or third-party audits.”
“Plex is a system that allows us to put just about everything we know about a customer, about our own production, about our products, and about the packaging into a form where we can keep track of it by lot number, by day, by production day, and we can access it very, very easily. It's one of the few systems that we found that lets us put in so much information we can use to make better decisions about our business,” said Lehman.
Lehman and his team find that the employees who have access to the ERP system have acquired a more criticial role. Shank’s has always valued its employees, and Plex has helped them understand why the tasks they complete are important to the overall business.
Lehman says its confidence is in the real-time data within Plex that helps Shank’s deliver what customers demand.
“Trust is important in our business. Our customers trust us to keep and make their private formulas according to their specifications. Because we trust the data in Plex, we can do what we do better.”